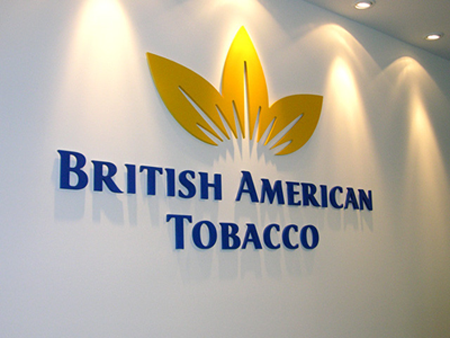
One sunny afternoon in April 2015, a Human Resource attaché escorted Folarin Shamsudeen from his office to the gate of the British American Tobacco company in Ibadan, Oyo State.
It was Mr. Shamsudeen’s last day at work.
It was also the beginning of a long drawn battle for justice with the tobacco company where he had worked for 12 years before he was shown the door that April.
Joining the British American Tobacco Nigeria Ltd in 2003 after being certified medically fit for the job, Mr. Shamsudeen, 35, said he left the company diagnosed with chronic sinusitis, chronic high blood pressure, and ingrown toenails – medical conditions he never had before his recruitment.
“At a meeting with the HR on April 31st, 2015, they told me that the company has the right to engage and disengage at any time, therefore my services will no longer be needed and I should submit the company properties in my care,” Mr. Shamsudeen said he was told after his health conditions began to affect his output.
Mr. Shamsudeen was among the several ex-staff of the British American Tobacco Nigeria who addressed journalists on Wednesday, in Lagos, seeking justice after being dismissed by the company for poor performance and health-related redundancy.
‘Poor working environment, recurrent infections’
Mr. Shamsudeen began working at BATN, Ibadan, on May 5, 2003, in the Primary Manufacturing Department. The department receives tobacco leaves, conditions them, cuts them into cut rags, re-dries them, before sending them to the Senior Manufacturing Department where they are packaged into real cigarettes.
He said the machines used for those tasks were obsolete and most of their operations were manual.
“In the Conditioning Department where I worked, we were to decase tobacco bales weighing 200 kilogrammes with our arms,” he said.
“The cartons are of two layers – the inner and outer layers. In the process of removing the case, dusts are usually dissipated from the dried tobacco of about 8 – 9 per cent moisture, when you open such there’ll be some cracks and dusts.
“It’s part of the procedure that we evaluate the tobacco bale very well. We are to smell it to perceive if it is mouldy, do some physical tests to see if it is infested with beetles, and if there is any foreign material, because sometimes in the farm they put slippers, stones, and all that.
“So we look around it, if it is mouldy, the product will be very irritating. So those ones that are mouldy, we reject them.”
After decasing the tobacco bale, Mr. Shamsudeen said, it goes into the conditioning silo, the Direct Conditioning and Casing (DCC) cylinder where the tobacco is boiled to a temperature of about 120 – 130 degrees Celsius so it can absorb water, and become pliable before it is cut.
“When it is coming out of the DCC, part of the procedure is that we have to do hand-feeling, to ensure that the tobacco is pliable and there is no paddy tobacco coming out.
“Paddy is the one that has not really absorbed water. So we’ll be doing hand-feeling to ensure the tobacco is well conditioned. In the process, some of us that are allergic to tobacco substance develop skin disease.”
Sometime in 2006, Mr. Shamsudeen said he began having a “perception of something rolling” in his ear. At the company clinic, an ENT surgeon advised him to carry out a simple procedure – put lukewarm water in a balloon and shoot it in the affected ear.
“Tobacco balls actually came out of my ear,” Mr. Shamsudeen recalled.
“I wonder how it got there. And if such things got into the ear, I wonder how much is in our system.”
When it’s time for an inspection by a government agency, according to Mr. Shamsudeen, work would be stopped for half a day to enable them clean the machines and the floor of the factory.
“People will be positioned at the door so that when the inspectors are coming, they will say ‘Start the machine,’ so that there will be less dust and steam. So that people will not see what we are actually going through, that’s the way they manage it.”
In 2008, Mr. Shamsudeen said he was diagnosed with chronic sinusitis at the University College Hospital, Ibadan.
“I was scheduled for treatment and placed on antibiotics and vitamin c and what they called steam aeration, to be managing it before my second visit.
“Unfortunately, before my second visit, BATN stopped their relationship with UCH, they said they want to cut costs. They arranged a doctor, they said he’s one of the consultants in UCH, just to see me in one corner. The man told me I would either do a procedure or continue with the palliative measure of steam aeration, taking antibiotics, vitamin c and all that.
“Some people had done that procedure and when they came back to the factory, their situation worsened. So I told the medical doctor that I would rather continue with the palliative measure until I’m confident of the procedure. I continued with the palliative measure until now.”
Sometime in 2011, Mr. Shamsudeen developed another medical condition called ingrown toenail, a condition when the side of the toenail grows into the flesh.
He said he did a Zadek Procedure – to remove the nail from the toe’s nail bed – at Bamby Specialist Hospital, Ibadan.
“After the procedure, the second big toe developed the same infection, I did the procedure again at Oluyoro Catholic Hospital. There, after the procedure, the doctor gave me the medical report where he stated that the ingrown toenail was as a result of chronic wearing of factory boots in a hot environment.”
In 2012, the ingrown toenail surfaced again, and Mr. Shamsudeen said he repeated the same procedure at Oluyoro Catholic Hospital.
The same condition returned in 2014.
“In fact, the fourth one, I didn’t want to go for the procedure again,” he said.
“But a resident doctor in the factory advised me to for it to avoid infection, so that the toe will not be finally cut off.”
A stiff neck incident
For Taofeek Alabi, in his ninth year of working with BATN as a Manufacturing Executive, he was diagnosed with cervical spondylosis, a form of neck-pain caused by age-related ‘wear and tear’ to bones and tissues. He began using a cervical collar, and later added a lumbar corset to it.
“Around 2013, I was going inside our office to drop a document,” Mr. Alabi, 40, recalled.
“On getting there, I noticed I couldn’t turn my neck to the left side again.”
Several visits to different hospitals in Ibadan only seemed to worsen Mr. Alabi’s condition.
At Oluyoro Catholic Hospital, the last of the hospitals he visited, the doctor gave him a letter advising the company that it would be “beneficial for the employee” if he’s moved from Production to another department.
In January this year, Mr. Alabi and his colleagues in the Production department were asked to report for medical evaluation. He went with the medical report advising that he be redeployed out of the department.
At the meeting, Mr. Alabi said his Head of Department asked him to go home, think, and make a choice if he still wants to work at the company because “there’s no vacancy in any department that they can take me to.”
“On Monday, when we were asked to come back, I went,” he continued.
“To my surprise, they came out with another thing. They wrote this letter on our behalf. It read: ‘Dear sir, Declaration of medical redundancy. I (I should fill my name), on my own behalf hereby confirm to British American Tobacco Nig. Ltd that I believe myself to be medically unfit for optimal performance of my role as a technician at BATN. I therefore request that BAT recognise me as being medically redundant, notwithstanding the details of all medical reports regarding my fitness for work which have been made available to me and to BATN by independent medical experts.’
“They wrote this and gave to me. I said ‘Ok, let me go with this and think about it.’ The HR manager said I can’t go with it. But I eventually snapped it. It was dated 25th January 2016. I refused to sign it. By February, they stopped my salary.”
Inhaler, nebuliser, ventolin, drugs
Before he joined the British American Tobacco Nigeria in 2003, Ayodele Awe was mandated to go for pre-work medical check-up at Teju Specialist Hospital, Ring Road, Ibadan.
He did, was certified medically fit, and was employed into the company’s Secondary Manufacturing Department, where cigarettes are packed into cases before they are sold.
“Some people were not employed because they were not certified medically fit,” Mr. Awe, 40, said.
However, four years into his job, a problem arose.
“One day, I discovered I had a tight chest – I had problems breathing, I was sweating profusely. The company’s ambulance was used to rush me down to Molly Specialist hospital, Idi-Ape, I was there for three days,” said Mr. Awe.
“On the third day, when I was discharged, I was talking to the doctor. I asked him what the cause was because all my life I had never had that kind of ailment before. He was asking me if my parents were asthmatic, or anybody in my family, I said I’m hearing that kind of ailment for the first time in my life. So since then I’ve been a canister-carrier.”
Five weeks after he was discharged from the hospital, Mr. Awe was rushed back there for the same ailment.
“The condition of the work – heat and a dusty environment are the things that trigger the ailment in me,” he said.
“They referred me to a specialist at UCH. There the guy said if they don’t want to pay me off, on medical grounds, they should change my department.”
In 2008, Mr. Awe’s job was changed from a machine operator to a quality inspector.
He said his new role exposed him further to the tobacco dust that triggers his attack.
“The company doctor called me, that do I want to go home or I still want to work? I said I want to work. He said they’re going to give me gadgets – nose mask, eye glass, all the thing that would shield me against dust and heat. Up till now, I never saw those things.”
After 12 years at BATN, Mr. Awe is now always equipped with an inhaler, nebuliser, canister of ventolin, and a cocktail of drugs.
I was in BATN for 12 years under that condition. I kept having a series of attacks. At a point in time, the doctor called me and asked if I was in BAT, I said yes. He said it’s better for me to leave there because of my condition.
“They diagnosed me, about three years ago, of having high blood pressure,” he said.
“How long will I continue like this? I find it hard to practise my profession again.
“My lawyer wrote to BATN to compensate me on the basis of my ailment, they wrote back that I had a pre-existing sickness before I joined the company. A company that before I joined, I was subjected to a rigorous medical test.”
A crushed cruciate
Unlike his colleagues, Ayodeji DaSilva’s ordeal at BATN began outside the company’s factory.
In 2010, during a periodic sporting activity organised for company staff, he tore his cruciate ligament.
“I went to Teju Hospital at Ring Road, Ibadan, I was diagnosed that I was going to be on a nine-month vigorous physiotherapy,” said Mr. DaSilva, 36, who joined BATN in 2007.
“When I went back to the office, my supervisor said I can’t go out of work for that long. Due to fear of losing my job, I had to continue work. But the pains were too much.”
Mr. DaSilva’s department runs 12-hour shifts, and he began wearing a knee support because he gets to stand for most of those hours.
One day, as he was descending a staircase at the office, his knee gave way. He rolled down the stairs, and passed out.
That was his last day at work.
“They abandoned me. They didn’t treat me. I went to different hospitals they said I need a knee filling, otherwise in the next five or ten years, my leg might be amputated. The two knees, I’m having cruciate ligament tear, both the anterior and posterior.”
“After a series of letters from Mr. DaSilva’s lawyer to BATN demanding money for his treatment; in 2014, the company sent him a letter of disengagement.”
“I have been cheated by BAT and abandoned,” Mr. DaSilva said.
“I can’t walk 10 metres without my knees giving in. I go everywhere with my knee support.”
BATN’s two-fold response
Barely three hours after their former staff finished laying out their grievances before journalists, BATN issued a scathing 530-word response accusing the employees of making demands that were unacceptable under Nigerian laws and ganging up with anti-tobacco NGOs.
In the statement, Oluwaseyi Ashade, Head of Corporate Affairs at BATN, said the company would not comment on the specifics of the case because one of the ex-employees had instituted a legal action against them.
“Our expectations will be that if there are any grievances with the process and procedures for disengagement, such grievance will be heard and determined under existing employee/employers dispute resolution mechanism including taking such grievances to the relevant Court and trusting the judicial system to hear both sides before making a judicial pronouncement,” Ms. Ashade said.
“We therefore note with bewilderment that the former employees involved anti-tobacco NGOs who have over the years openly advocated for the closure of the legal tobacco industry in Nigeria to suddenly become the vanguard for tobacco employees.”
About 24 hours later, the tobacco company issued a second statement, this time a 216 word response that adopted a conciliatory tone.
The company said it is committed to providing a great and safe work environment because it understands the importance of its workers and their welfare in the continued growth and sustainability of BATN.
“These new allegations have been made by a group of former employees who left BAT Nigeria between 2015 and 2016,” said Freddy Messanvi, Legal and External Affairs Director at BATN.
“We take these kinds of allegations seriously and are currently investigating them as part of our strict adherence and commitment to workplace safety, which has resulted in us maintaining a zero incidence of work place injuries for the past eight years.”
“We adhere strictly to our Environment, Health & Safety policy implementation, which applies to employees, contractors, visitors and suppliers in our Factories and our offices.
“We also abide by the local laws and are compliant with not just the local regulations as required by all relevant local agencies but we also benchmark ourselves against the requirements for labour practices globally, such as the OECD guidelines for Multinational Enterprises as provided for by our parent company.”
But the former employees maintained that BATN’s work environment fall below the accepted standard and called on the government to help them get a just compensation from the company.
“We want the government to call this BAT to order,” Mr. Shamsudeen said.
“They are not operating as a responsible organisation in Nigeria. How can they be using nose-masks that are used in banks and eateries in a tobacco factory?”
PremiumTimes
END
Be the first to comment